Frânsk sinne-enerzjysynstitút INES hat nije PV-modules ûntwikkele mei thermoplastyk en natuerlike fezels dy't yn Jeropa komme, lykas flaaks en basalt.De wittenskippers binne fan doel de miljeufootprint en it gewicht fan sinnepanielen te ferminderjen, wylst se recycling ferbetterje.
In recycled glêzen paniel oan 'e foarkant en in linnen gearstalde op' e rêch
Ofbylding: GD
Fan pv tydskrift Frankryk
Undersikers fan Frankryk's National Solar Energy Institute (INES) - in ôfdieling fan 'e Frânske Kommisje foar Alternative Energien en Atomic Energy (CEA) - ûntwikkelje sinnemodules mei nije bio-basearre materialen oan' e foar- en efterkant.
"Om't de koalstoffoetôfdruk en de analyse fan 'e libbenssyklus no essensjele kritearia wurden binne yn' e kar fan fotovoltaïske panielen, sil de boarne fan materialen yn 'e kommende jierren in krúsjaal elemint wurde yn Jeropa," sei Anis Fouini, de direkteur fan CEA-INES , yn in ynterview mei pv tydskrift Frankryk.
Aude Derrier, de koördinator fan it ûndersyksprojekt, sei dat har kollega's hawwe sjoen nei de ferskate materialen dy't al besteane, om ien te finen dy't modulefabrikanten koe meitsje om panielen te produsearjen dy't prestaasjes, duorsumens en kosten ferbetterje, wylst de miljeu-ynfloed ferleegje.De earste demonstrator bestiet út heterojunction (HTJ) sinnesellen yntegrearre yn in all-composite materiaal.
"De foarkant is makke fan in glêsfezelfolle polymeer, dy't transparânsje leveret," sei Derrier."De efterkant is makke fan komposite basearre op thermoplastyk wêryn in weven fan twa fezels, flaaks en basalt, yntegreare is, wat meganyske sterkte leveret, mar ek bettere wjerstân tsjin focht."
It flaaks komt út Noard-Frankryk, dêr't it hiele yndustriële ekosysteem al oanwêzich is.It basalt komt earne oars yn Europa en wurdt weefd troch in yndustriële partner fan INES.Dit fermindere de koalstofôfdruk mei 75 gram CO2 per watt, yn ferliking mei in referinsjemodule fan deselde krêft.It gewicht waard ek optimalisearre en is minder as 5 kilogram per fjouwerkante meter.
"Dizze module is rjochte op PV op it dak en yntegraasje fan gebouwen," sei Derrier.“It foardiel is dat it natuerlik swart fan kleur is, sûnder in efterblêd nedich.Op it mêd fan recycling is de skieding fan de lagen technysk ek ienfâldiger, troch thermoplasten, dy’t wer smelt wurde kinne.”
De module kin makke wurde sûnder aktuele prosessen oan te passen.Derrier sei dat it idee is om de technology oer te dragen oan fabrikanten, sûnder ekstra ynvestearring.
"De iennichste ymperatyf is om friezers te hawwen om it materiaal op te slaan en net it harsferbiningsproses te begjinnen, mar de measte fabrikanten brûke hjoed prepreg en binne hjir al foar útrist," sei se.
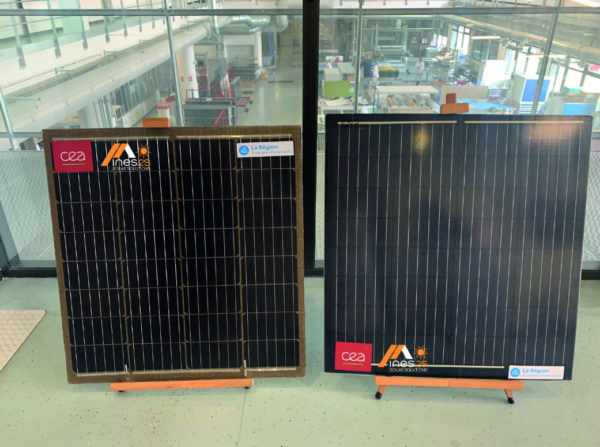
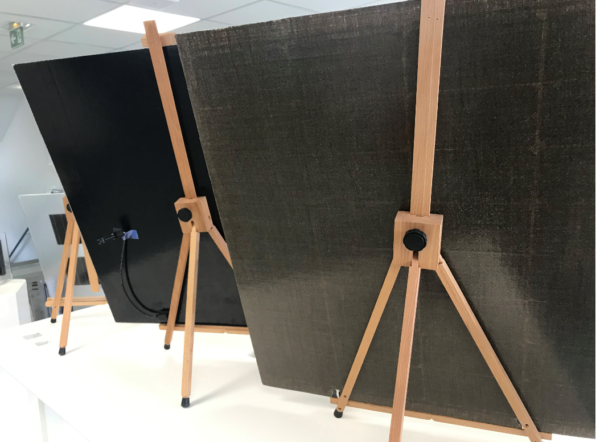
"Wy wurken oan it twadde libben fan glês en ûntwikkele in module makke fan opnij brûkt 2,8 mm glês dat komt fan in âlde module," sei Derrier."Wy hawwe ek in thermoplastyske ynkapseling brûkt dy't gjin cross-linking nedich is, dy't dêrom maklik te recyclearjen sil wêze, en in thermoplastyske komposyt mei flaaksfaser foar ferset."
It basaltfrije efterkant fan 'e module hat in natuerlike linnenkleur, dy't foar arsjitekten bygelyks estetysk nijsgjirrich wêze kin yn termen fan gevelyntegraasje.Derneist toande it INES-berekkeningsark in 10% reduksje yn 'e koalstoffoetôfdruk.
"It is no ymperatyf om de fotovoltaïske leveringsketten te freegjen," sei Jouini.“Mei help fan de regio Rhône-Alpes yn it ramt fan it Ynternasjonaal Untwikkelingsplan binne wy dêrom op syk nei spilers bûten de sinnesektor om nije thermoplasten en nije fezels te finen.Wy hawwe ek neitocht oer it hjoeddeiske laminaasjeproses, dat tige enerzjy-yntinsyf is.”
Tusken de druk-, de parse- en de koelfase duorret de laminaasje meastentiids tusken de 30 en 35 minuten, mei in wurktemperatuer fan om de 150 C oant 160 C.
"Mar foar modules dy't hieltyd mear eko-ûntwurpen materialen omfetsje, is it nedich om thermoplastyk te transformearjen op sawat 200 C nei 250 C, wittende dat HTJ-technology gefoelich is foar waarmte en net mear dan 200 C moat," sei Derrier.
It ûndersyksynstitút wurket gear mei Roctool-spesjalist foar ynduksje-thermokompresje basearre yn Frankryk, om syklustiden te ferminderjen en foarmen te meitsjen neffens de behoeften fan klanten.Tegearre hawwe se in module ûntwikkele mei in efterkant makke fan polypropyleen-type thermoplastyske komposit, wêryn recycled koalstoffezels binne yntegreare.De foarkant is makke fan thermoplastyk en glêstried.
"Roctool's induksje-termokompresjeproses makket it mooglik om de twa foar- en efterplaten fluch te ferwaarmjen, sûnder 200 C te berikken yn 'e kearn fan' e HTJ-sellen," sei Derrier.
It bedriuw beweart dat de ynvestearring leger is en dat it proses in syklustiid fan mar in pear minuten kin berikke, wylst minder enerzjy brûkt wurdt.De technology is rjochte op gearstalde fabrikanten, om har de mooglikheid te jaan om dielen fan ferskate foarmen en maten te produsearjen, wylst lichtere en duorsumer materialen yntegrearje.
Post tiid: Jun-24-2022